elcome dear friends of protection and control engineering. In our new guest article, we present you an up-to-date solution of the TEN Thuringian Energy Networks for the modernization of their networks. We thank you for the guest contribution of Dipl.-Ing. (FH) Karsten Natus, branch marketing; and Bernd Schairer, Industrial Management Energy; Phoenix Contact Germany GmbH.
Robust plug-in test system facilitates testing of protective devices
As power grids become smarter and more efficient in the course of modernization, reliability also plays an important part. TEN Thüringer Energienetze, a German grid operator, makes advances in modernization by means of Fame 2. Phoenix Contact's robust measuring and testing system allows testing to be performed quickly and reliably even during active operation (Figure 1).
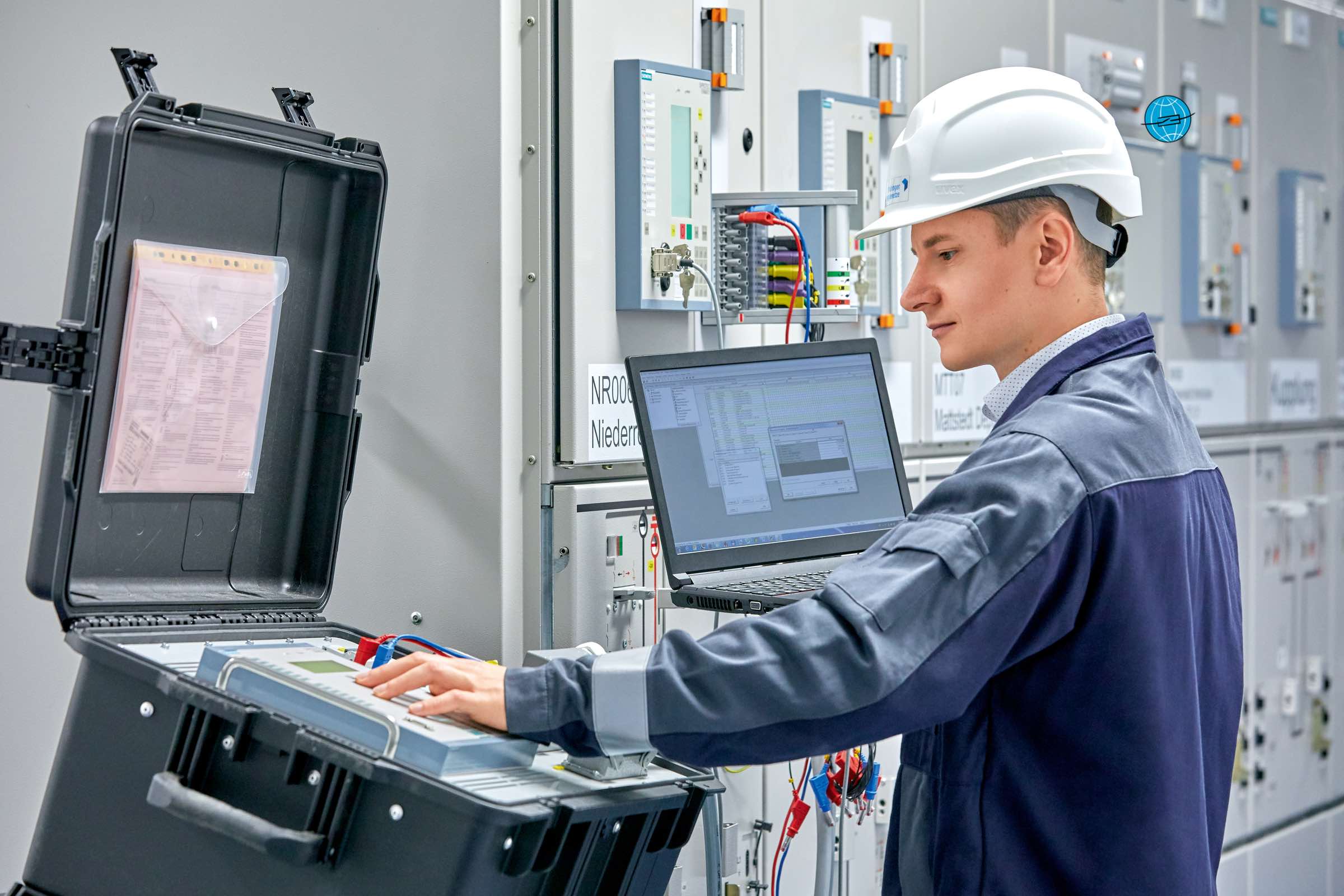
TEN Thüringer Energienetze GmbH & Co. KG, headquartered in the city of Erfurt, is the largest grid operator in the German state of Thuringia. By operating an electricity and gas network of around 40,000 kilometers in length, the company supplies energy to more than 1.1 million people and to businesses in Thuringia and parts of Saxony and Saxony-Anhalt. More than 16,000 decentralized energy generators also supply TEN's grid. Being part of an organization called “Arbeitsgemeinschaft Flächennetzbetreiber Ost” – ARGE FNB Ost for short - TEN actively contributes to the country's energy transition.
Decentralized locations foster close proximity to local customers
At the 18 locations, a staff of 700 employees works on the servicing and maintenance of the 110-kV grid and the low-voltage grid with its 90 substations, on the construction of transformer stations, the supply of temporary power to construction sites, and on the installation of power meters. The company's decentralized organization ensures a close proximity to the customers and a high degree of grid reliability (figure 2).
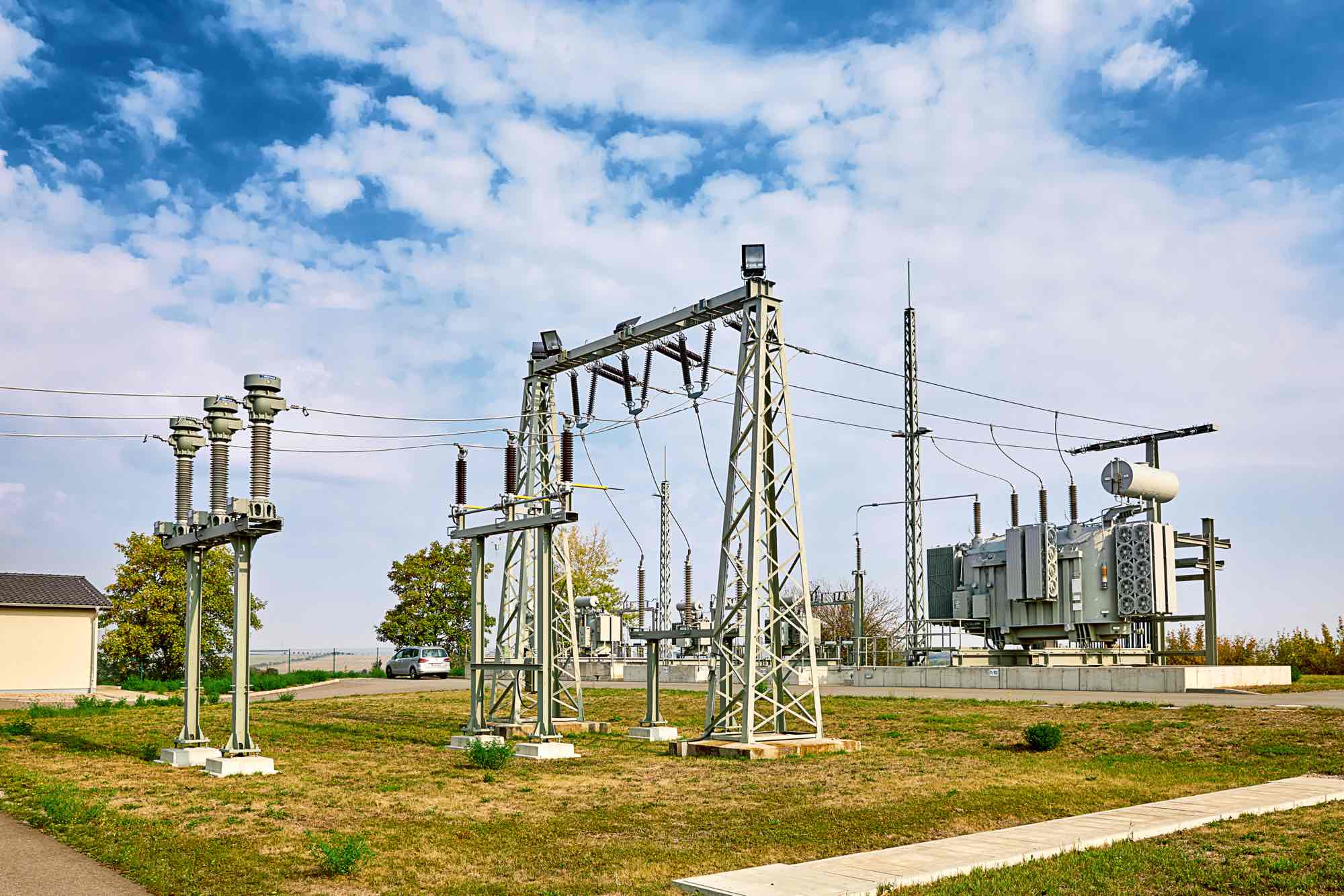
As a fundamental requirement for a high degree of reliability, every malfunction must be detected immediately and resolved quickly. “To this end, digital mains protection relays permanently monitor the energy flows from the transformer and distribution substations by means of current and voltage transformers,” Heiko Kraut, Department Manager at TEN, explains. “When an error occurs, corrective actions – such as the switching of lines – can be initiated immediately.” (Figure 3)
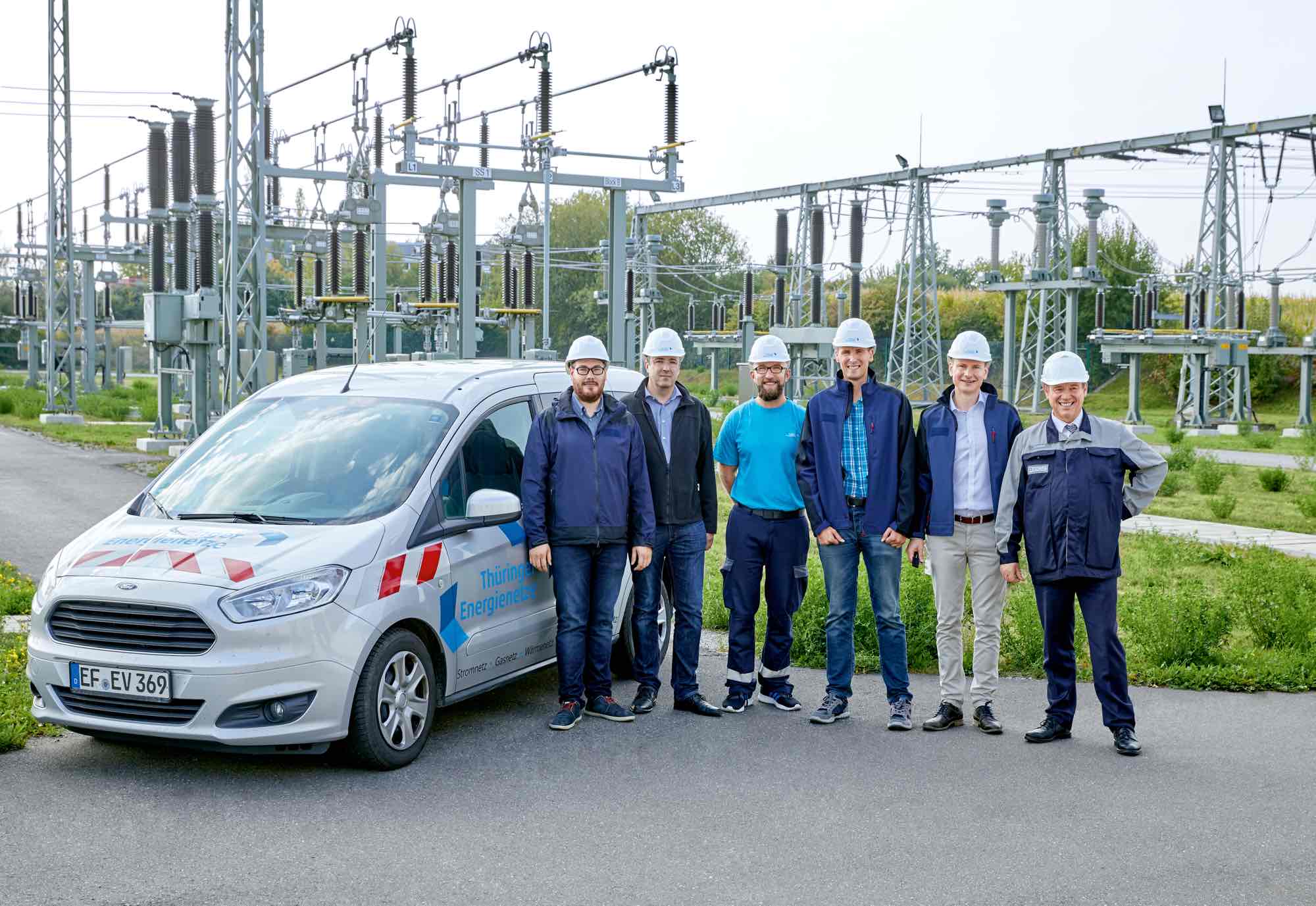
René Müller, specialist for safety technology in medium-voltage grids; Dipl.-Wirt.-Ing. Heiko Kraut, Department Manager; Tobias Taubert, engineer and specialist for secondary technology; Markus Funke, specialist for safety technology in medium-voltage grids; Paul Sicker, specialist for safety technology in high-voltage grids; and Bernd Schairer from Industry Management Energy at Phoenix Contact Deutschland GmbH
Tried and tested – but also outdated
To ensure that the distribution networks operate reliably, the safety equipment itself also needs to be monitored. Therefore, all mains protection relays in the transformer and distribution substations undergo regular documented protection tests.
In Germany's eastern states, protection tests are commonly done by means of plug-in test systems. Like other energy providers, TEN had been using quite a lot of different plug-in test systems – all with their design-specific particularities. “The older systems had test plugs that required the use of both hands to disconnect them,” Mr. Kraut remembers. “This could cause the test-plug device to twist, and lead to errors during protection testing.” The reason behind it is that multi-position plugs, when they are plugged in or pulled out at an angle, lead to time-delayed switching operations in the plug-in test socket. Mr. Kraut: “The plug-in test conductors in the switchgear panel also had no external protection against dirt or touching, lacking a blind cover.” The plug-in test sockets weren't protected against dust or dirt at all.
Furthermore, some systems had their weaknesses with regard to the connection methods. To allow for the connection of conductors, for example, they required an unprotected ring or fork-type cable lug, which then needed to be covered by a Plexiglass sheet as a means of protection against accidental contact.
“We were looking for a plug-in test system significantly more convenient to handle, which offered more safety during wiring operations,” Mr. Kraut explains. The testing system of a different manufacturer proved to be even more instable. Mr. Kraut: “It was very difficult to evenly pull out the 19-pos. test plug of the plug-in test socket. The delicate snap-in latches broke off easily, and the plug-in test socket was not covered during normal operation.”
Safe working conditions and error-free protection testing
Today, in the substation in the city of Apolda, TEN uses Fame 2, Phoenix Contact's modular plug-in test system. The test device is contacted by means of the 14-pos. test plugs in one single connecting operation. There is no need for any disconnect slides to be actuated one by one, which eliminates a common cause of errors (figure 4).
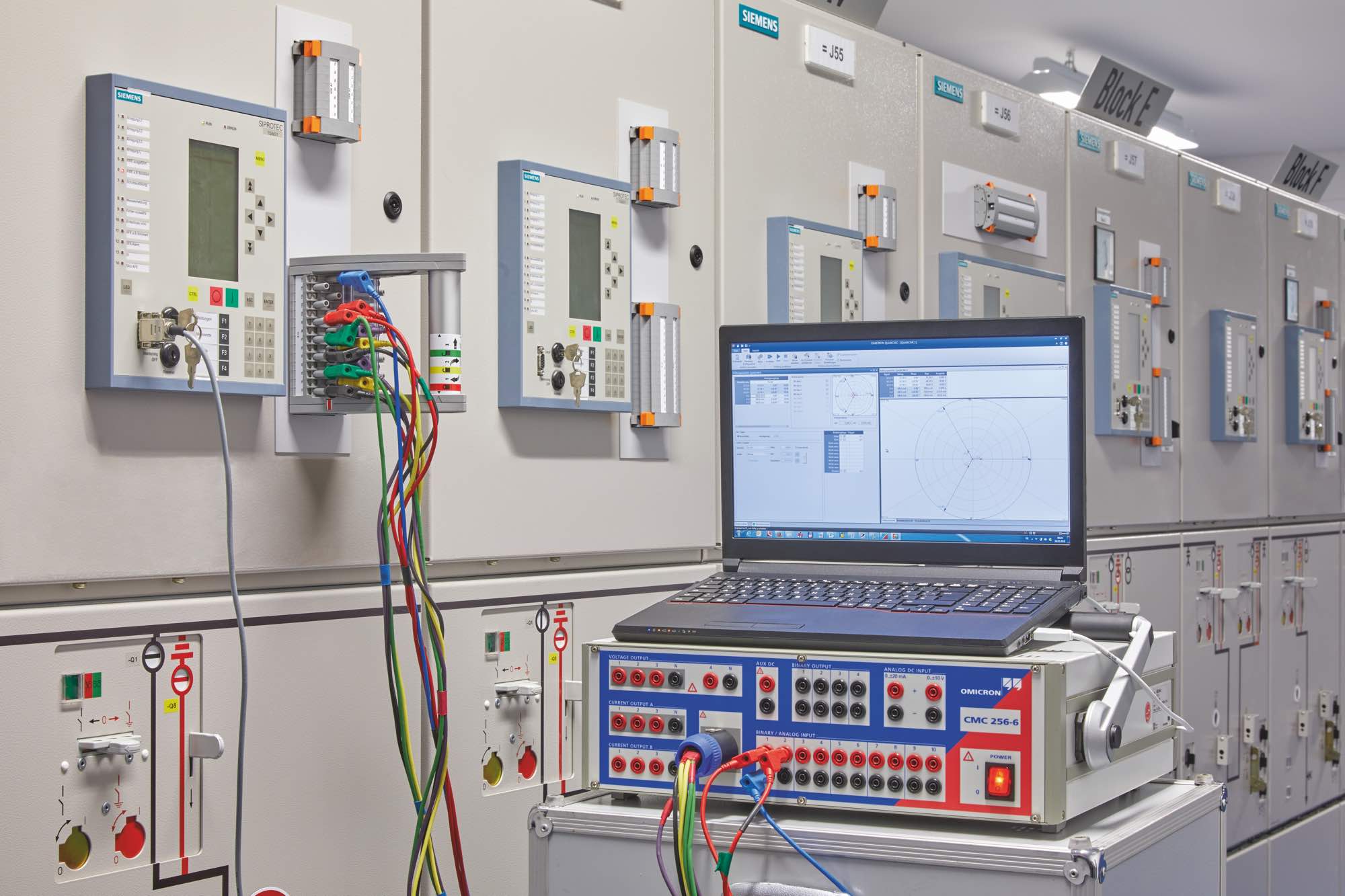
The snap-in mechanism integrated into the Fame rotary handle ensures that the plug can be pulled out straightly and evenly. A status indicator window using traffic light colors simultaneously indicates the locking state (figure 5).
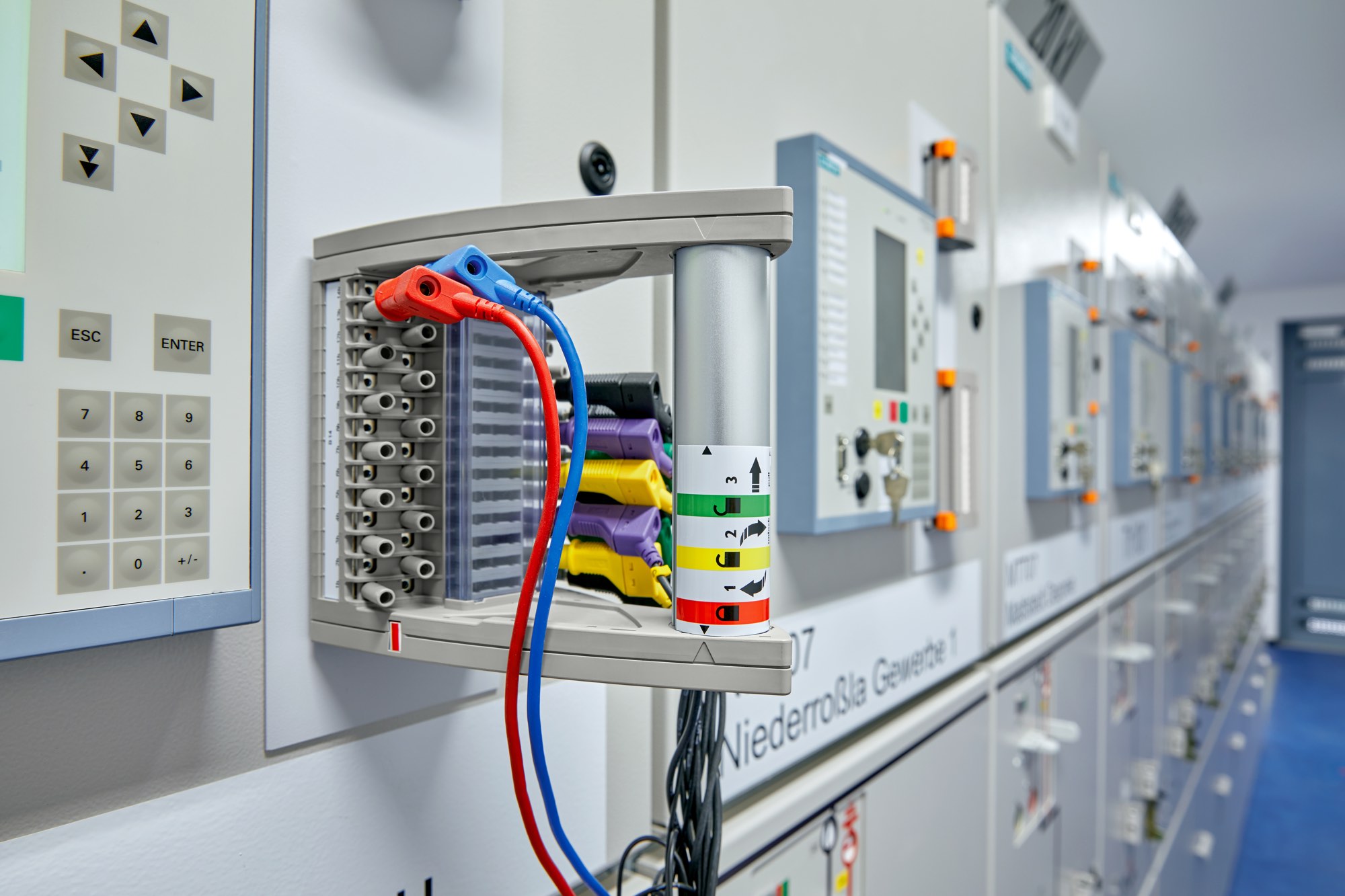
The Fame plug-in test system allows the setup of test sockets that are individually adapted to match different tests scenarios – such as IDMT protection or distance protection. A range of accessories including color-coded 1-pos. to 4-pos. service test plugs further facilitates the work. For example, the single-pole plug can be used to make individual measurements, or to disconnect the OFF signal to the high-voltage switch from the protective device, without affecting other functions. “The integrated rotary handle, the guide lugs, the coding options, the visibility of the plugged-in bridges within the plug, and, finally, the mechanism for locking the plug-in test system exactly meet our requirements,” Paul Sicker, high-voltage technology specialist at TEN, adds. “Thanks to the Fame 2 plug-in test system, we can now perform protection tests in a way that is safe and without errors.”
Testing protective devices without disconnecting them
A large portion of the more than 16,000 decentralized power generating facilities – including numerous PV systems and wind turbine generators – is connected to the medium-voltage grid. Testing the associated grid protection devices requires timely, careful, extensive planning and organization. However, past experiences have shown that in spite of all preparatory measures, disconnections on schedule are often canceled on short notice – and scheduled grid protection tests need to be postponed. The substations in TEN's network area are the exception here. However, the situation described above is likely to occur more frequently in the future, due to more decentralized power generating facilities being integrated specifically into the medium-voltage grid.
The solution in this case is an interim protective solution developed by TEN (cf. figure 1, lead image). By connecting it to the Fame 2 plug-in test system by means of the standardized plug-in test socket, the interim protective solution ensures mains protection for the outgoing medium-voltage line to be tested. The interim protective device is automatically looped in by simply plugging the test plug into the plug-in test socket. At the same time, the protective device to be tested is connected to the test device. The mains protection for the concerned line section or transformer is thus maintained during testing.
Device replacement made easy
If a protective device fails or causes a fault, a service technician can replace it via the Fame 2 plug by an interim protective device, even outside of normal working hours. “By means of the spare device, the fault is eliminated quickly, and grid disturbances are minimized,” Mr. Sicker says. “The next day, a protection engineer can replace the faulty device without affecting grid reliability.”
While numerous grid operators prefer their own specifications with individual assignments, the company from Thuringia has opted for the specification of VDE. Thanks to its modularity, the Fame 2 plug-in test system works well with both approaches. “We were convinced by the Fame 2 plug-in test system particularly because of its well thought-out design,” Mr. Kraut says. “Our test results have confirmed all expectations.”
Summary: company-wide use
Thanks to the replacement of TEN's existing plug-in test system by Phoenix Contact's Fame 2 plug-in test system, testing of the protective devices has become safe and error-free. The advantageous design of the plug-in test system is the basis for an even higher reliability of the networks, and also for standardized protective device tests across the entire area supplied by TEN. “Modernizing the substation in Apolda was our pilot project”, says Mr. Kraut. “Because of the discontinuation of some formerly used products, and due to the unacceptable price developments on the market, we decided to choose Phoenix Contact's Fame 2 plug-in test system in all modernization and construction projects.”
We thank you for the successful guest contribution. For all readers who continue to be interested in Fame, we have already reported extensively in previous articles (just click on the pictures below):
The sniff-test | Test Plug Systems
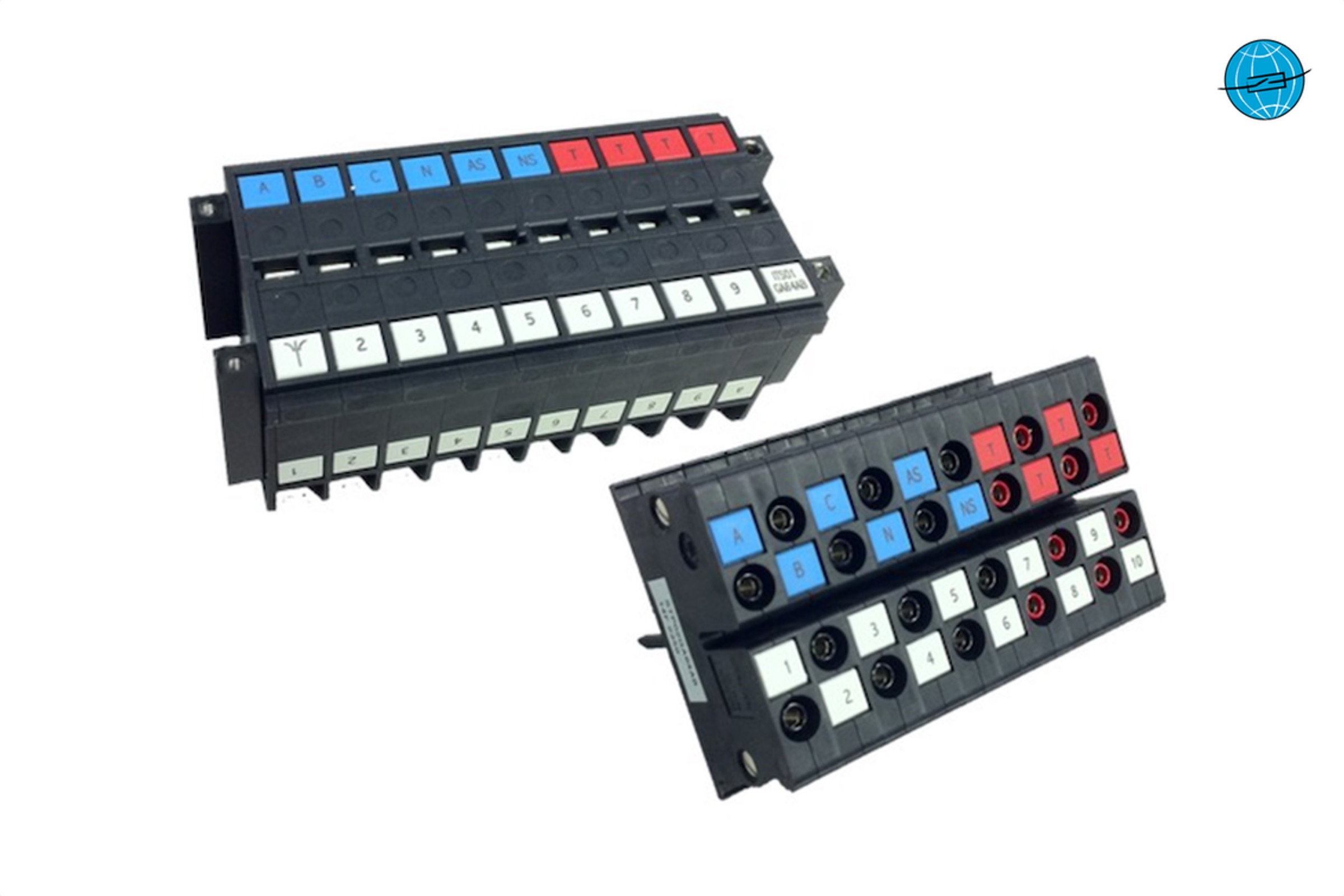
Increase of safety with FAME
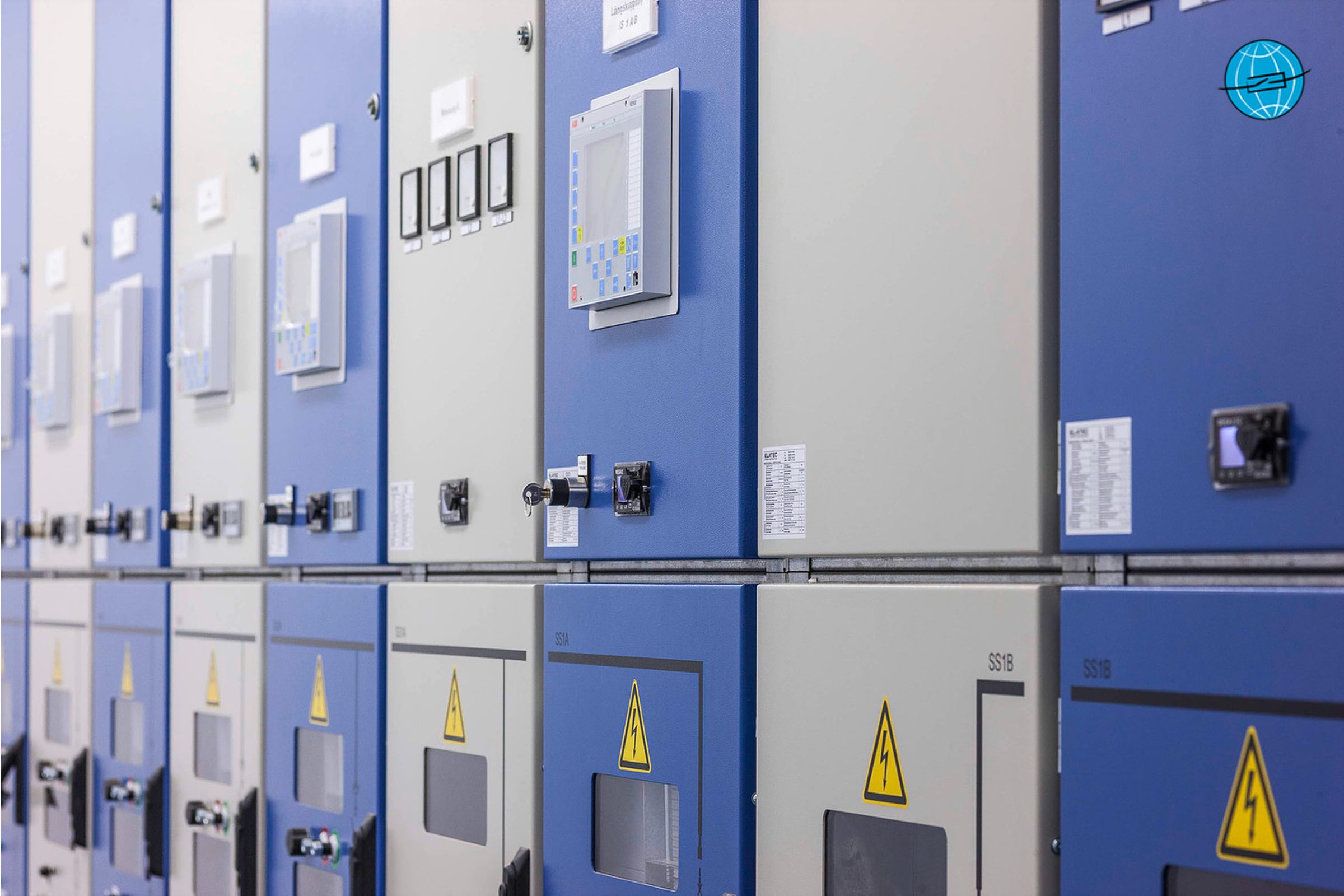